鋁型材自動裝框設備的應用
1、引言:
在鋁型材加工行業中,擠壓生產線中產品定尺據切后,一般是人工將產品由鋸床輥道上抬到專用料框中,此方法人力勞動強度大,人工需求量大,且產品質量受人為因素影響。近年來國內高速發展大截面高線密度的工業鋁型材,成品重量大大增加,而且產品類型與形狀復雜多樣,靠人工搬運是不可能的。針對這一現狀,鑫臺銘應用一種鋁型材自動裝框設備,實現裝框自動化,降低人力勞動強度,減少人員配置,降低生產成本,有利地避免了鋁型材在傳輸時表面刮花碰傷等損傷問題,提高成品率;同時有效地解決由于鋁型材重量增加帶來的傳輸問題。
2、鋁型材自動裝框設備的結構及工作原理:
2.1 設備結構。
自動裝框設備的結構如下圖1所示,包括機架1、傳動系統一2、料框3、輸送臂9和鋸床輥道10;其中傳動系統一包括傳動軸4、齒輪一5、齒輪二6、齒輪三7和齒條8。下圖1所示的結構中傳動系統一在電動機的驅動下只是帶動輸送臂上下運動,在圖紙的垂直。
2.2 設備工作原理。
自動裝框設備的工作原理:在電動機的驅動下經過傳動系統的傳動,使輸送臂運動,從而帶動其上面的鋁型材移動進行裝框,具體工作過程如下:
2.2.1 傳動過程。
電動機驅動傳動軸轉動,傳動軸帶動齒輪一轉動,接著帶動與之嚙合的齒輪二轉動,齒輪二帶動兩邊嚙合的齒條移動,然后帶動輸送臂運動,同時也帶動齒輪三轉動,齒條在齒輪二、三之間往復移動。
2.2.2 裝框過程。
首先輸送臂在傳動系統一的帶動下往上運動,把鋁型材往上頂出鋸床輥道;然后傳動系統二使輸送臂往左運動,鋁型材離開鋸床上方至料框正上方;接著傳動系統一反向傳動使輸送臂往下運動,鋁型材慢慢地進入料框內;傳動系統二反向傳動帶動輸送臂往右運動,當鋁型材接觸料框底部后,其重量逐漸施加在料框上,輸送臂與鋁型材、料框脫離,回到初始位置,鋁型材穩定放置于料框內,自動裝框完成。
3、設備安裝使用注意事項:
3.1 傳動齒條需采用韌性與耐磨性好的高分子材料,否則使用中容易斷裂磨損;
3.2 輸送臂的制造材料需是不銹鋼,其表面要保持平整光亮,不然鋁型材表面質量容易變差;
3.3 料框放置位置需要與輸送臂的位置相對應,防止輸送臂在回撤的過程中被料框阻擋而無法撤回;
3.4 不斷調試裝框速度,同時設備安裝時控制輸送臂的重量,使裝框速度與生產速度匹配,并且裝框過程鋁型材穩定在輸送臂上;
3.5 每個輸送臂只能同時由一個電動機驅動的傳動系統帶動,設備在使用前需要將鋁型材放置在輸送臂上壓一段時間,并不斷地調試與重新安裝輸送臂的位置,避免鋁型材在裝框時移動或是表面不在一個平面上;
3.6 每框鋁型材必須裝滿框面以下5mm的位置,每排鋁型材間要放墊條隔開,充分利用料框內空間且保證每框料之間有一定的間隙,循環熱風可以到位,確保加熱效果良好;
3.7 在裝框過程中遵循厚重型材在下面,輕薄型材在上面的原則,長短不一致的鋁型材原則上不能裝在同一料框內,特殊情況下需要混裝時,應采取長下短上的裝框方式,裝好框后用彩條布蓋好后及時轉至中轉倉進爐時效。
4、鋁型材自動裝框設備的優點:
與傳統的人工搬運鋸切后的鋁型材至料框內相比,自動裝框設備有如下優點:
4.1 投入資金少,設備使用后可以減少車間配置人員,降低生產成本,設備安裝在距切輥道下面,幾乎不占用車間面積,自動化程度高,操作簡單;
4.2 避免工人兩端抬料時造成鋁型材的彎曲、扭擰、擦傷與碰傷等損傷問題,提高成品率;
4.3 采用優質不銹鋼材料加工的輸送臂,顯著增加其承載能力,可以滿足高線密度工業鋁型材的運輸要求,同時輸送臂的尾端截面呈梯形,鋁型材在脫離輸送臂時緩慢穩定,不會造成鋁型材擦傷或撞傷;
4.4 鋸床輥道上采用多根、接觸面窄的毛氈帶,根數多,牽引力大,有利于鋁型材傳送,接觸面窄減少了由于摩擦造成的型材表面刮花。
5、結束語:
鋁型材自動裝框設備的研究應用,有效地解決了鋁型材成品在據切后的裝框人力勞動強度高、鋁型材裝框時易損傷、高線密度工業鋁型材的運輸問題;設備具有自動化程度高,操作簡單,降低生產成本與提高成品等特點。隨著鋁型材自動裝框設備的不斷完善,其將廣泛地應用于鋁型材擠壓生產線中,為鋁型材加工行業帶來較大的效益。
相關資訊
推薦產品
最新資訊 News
聯系我們 Contact Us
-
聯系人:劉大軍
手 機:18138436465
電 話:0755-28365643
傳 真:0755-89636058
郵 箱:33434175@qq.com
地 址:深圳市龍崗區坪地街道六聯社區鵝公嶺西路6-12號
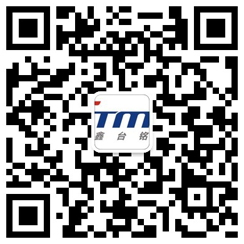